Welding in Steel Pipe Manufacturing: HFW vs. ERW
You are here: Home>Industry Information>Welding in steel pipe manufacturing: HFW vs. ERW
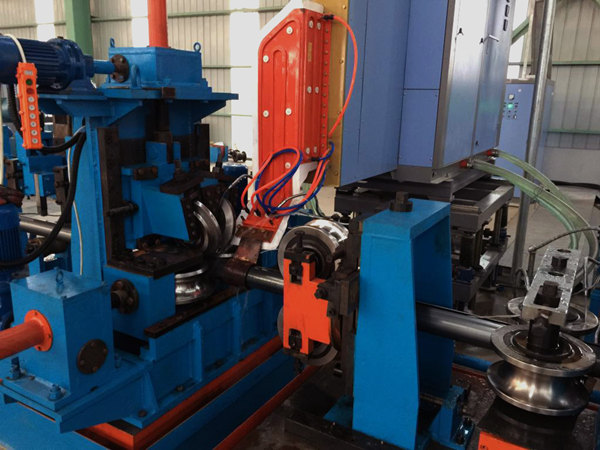
Introduction
In the field of steel pipe manufacturing, distinguishing between High Frequency Welding (HFW) and Electric Resistance Welding (ERW) is crucial for industry professionals. Both methods are integral to the production process, each with unique operational principles and applications. This comprehensive guide explores the differences between HFW and ERW, providing detailed insights into their technical aspects and practical implications across various industrial sectors.
Electric Resistance Welding (ERW)
Electric Resistance Welding (ERW) employs resistance heating to join metals. Electrodes apply pressure after assembly, facilitating welding through resistance heat generated by current passing through the joint’s contact surfaces. ERW is highly regarded for its precision in straight seam applications, offering reliable welds essential for industries requiring robust structural integrity.
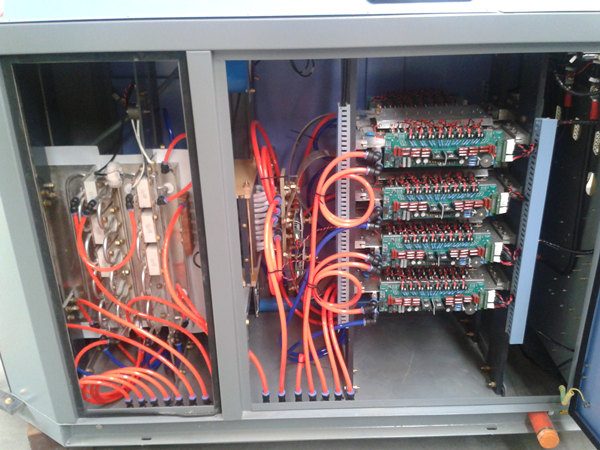
High Frequency Welding (HFW)
High Frequency Welding (HFW) utilizes high-frequency currents to concentrate energy on the workpiece’s surface. This process rapidly heats and melts adjacent steel plate edges, enabling seamless butt joints in a fraction of the time required by traditional methods. HFW’s efficiency and speed make it ideal for high-volume manufacturing environments where production timelines are critical.
Comparative Analysis: ERW vs HFW
The primary distinction between ERW and HFW lies in their welding techniques and applications. ERW’s reliance on resistance heating ensures precise welds suitable for straight seams and critical structural applications. In contrast, HFW’s use of high-frequency currents offers accelerated welding speeds without compromising weld quality, making it advantageous for projects prioritizing efficiency and rapid production cycles.
Applications and Advantages
ERW is preferred for its ability to produce high-quality welds, meeting stringent industry standards for structural integrity and performance. Industries such as construction, automotive, and oil & gas rely on ERW for its consistent weld quality and reliability. HFW excels in applications requiring rapid production, such as in manufacturing pipelines, where seamless joints and high production rates are essential.
Here’s a simplified comparison table between High Frequency Welding (HFW) and Electric Resistance Welding (ERW) in steel pipe manufacturing:
Aspect | High Frequency Welding (HFW) | Electric Resistance Welding (ERW) |
Principle | Uses high-frequency currents to heat and weld the metal | Uses resistance heating to weld the metal |
Speed | Rapid welding process | Slower compared to HFW |
Application | Ideal for high-volume production, quick turnaround times | Suitable for straight seam welding, precise applications |
Energy Efficiency | Generally higher energy consumption due to high-frequency currents | Generally lower energy consumption |
Weld Quality | Excellent for seamless joints, suitable for various thicknesses | High-quality welds, reliable for structural applications |
Industry Use | Pipeline manufacturing, automotive, high-speed production | Construction, oil & gas, industries requiring precision |
Advantages | Speed, efficiency, seamless joints | Precision, reliable welds, structural integrity |
Disadvantages | Higher energy consumption, initial setup costs | Slower speed compared to HFW, limited to straight seams |
Common Applications | Pipelines, large-scale manufacturing | Structural applications, pipes requiring precision |
Frequently Asked Questions (FAQs)
Q: What are the primary advantages of ERW over HFW?
A: ERW is known for its precise welds and suitability for straight seam applications, offering exceptional weld quality and reliability.
Q: When should HFW be chosen over ERW?
A: HFW is preferred for projects requiring rapid welding speeds and high production efficiency, making it ideal for industries with tight production schedules.
Q: How do ERW and HFW differ in terms of energy consumption?
A: ERW typically consumes less energy compared to HFW due to its reliance on resistance heating rather than high-frequency currents.
Conclusion
Understanding the nuances between High Frequency Welding (HFW) and Electric Resistance Welding (ERW) is essential for professionals in the steel pipe manufacturing sector. Each method brings distinct advantages: ERW offers precision and reliability, while HFW provides speed and efficiency. By choosing the appropriate welding technique based on project requirements, manufacturers can optimize production processes and achieve superior weld quality in steel pipe manufacturing.
Products
- 457mm FFX ERW Tube Mill
- 34mm*6.5mm Pipe Mill
- Roller Quick Change System Tube Mill
- Large Diameter Direct Forming Square Tube Mill
- TD 38 Tube Mill(12-38mm)
- TD 50 Tube Mill(25-63mm)
- TD 76 Tube Mill(32-89mm)
- TD 114 Tube Mill(42-119mm)
- TD 127 Tube Mill(42-127mm)
- TD 219 Tube MIll(89-219mm)
- TD 273 Tube MIll(114-273mm)
- TD 325 Tube MIll(127-325mm)
- Slitting Line
- Cut to Length Line
- Cold Roll Forming Machine
Related Products
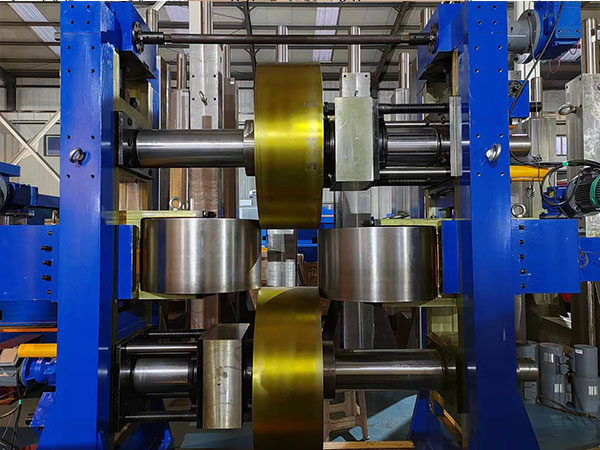