What is the Process of a Tube Mill | How Are Steel Pipes Made?
You are here: Home>Industry Information>What is the Process of a Tube Mill | How Are Steel Pipes Made?
What is a Pipe Mill?
A pipe mill, often referred to as a tube mill, is a manufacturing facility where steel pipes are produced through a series of processes. These mills are integral to the steel production industry, as they provide the essential infrastructure for various industries, including construction, automotive, and energy sectors. Tube mills typically use a combination of machinery and skilled labor to convert raw materials into finished pipes, which can vary in size, shape, and material based on the intended application.
The tube mill process is a systematic series of steps that transform steel coils into finished pipes. The process begins with the uncoiling of steel strips, which are then fed into the forming section of the tube mill. Here, the strips are shaped into a circular or square cross-section, depending on the desired pipe shape.
Next, the edges of the formed tube are welded together using techniques like Electric Resistance Welding (ERW) or High-Frequency Induction Welding (HFIW). The welded tube then undergoes sizing, where it is calibrated to precise dimensions. This is followed by cooling, straightening, and cutting to the required lengths. Finally, the pipes undergo quality checks to ensure they meet industry standards.
What is the Process of Manufacturing Steel Pipes?
The process of manufacturing steel pipes in a tube mill can be broken down into several stages:
Raw Material Preparation: Steel coils are loaded onto the uncoiler and prepared for processing.
Forming: The steel strip is gradually formed into a circular or square shape through a series of rollers.
Welding: The edges of the formed pipe are welded together using high-frequency welding techniques, ensuring a strong and durable seam.
Sizing and Shaping: The welded pipe is passed through sizing mills, where it is shaped and calibrated to the desired dimensions.
Cooling and Straightening: The pipe is cooled and straightened to ensure it meets the required specifications.
Cutting and Finishing: The pipes are cut to the required lengths and undergo finishing processes, such as threading or coating, depending on the application.
Quality Inspection: Each pipe is inspected for quality, ensuring it meets industry standards and customer specifications.
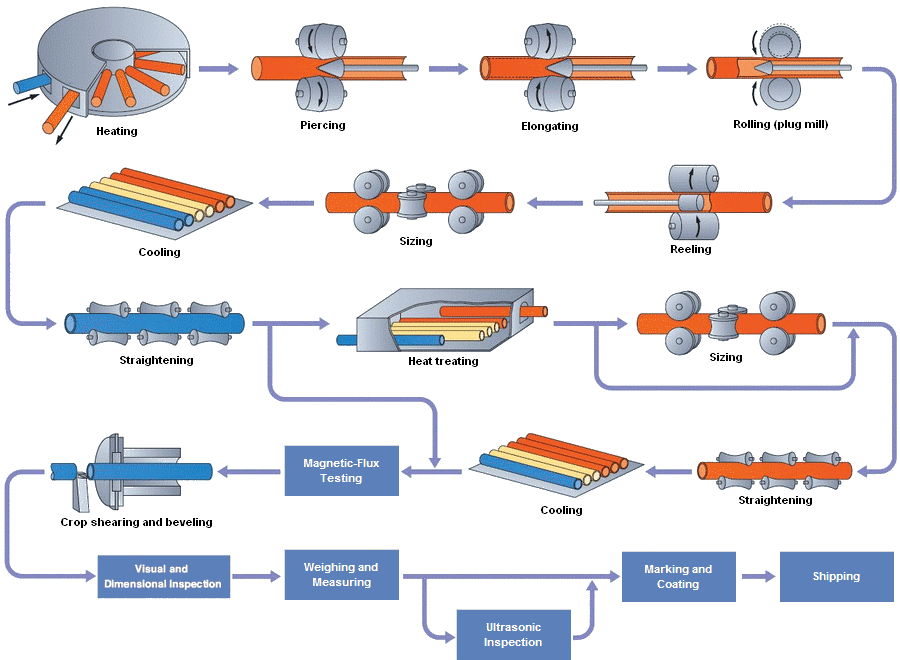
Choose the Right Tube Mill Supplier
Selecting the right tube mill supplier is crucial to ensuring the success of your production line. A reliable supplier will provide not only high-quality machinery but also the necessary support and services to ensure smooth operations. When choosing a supplier, consider factors such as their industry experience, the range of products offered, and after-sales services. Additionally, look for suppliers who can provide customized solutions tailored to your specific needs.
Additional Considerations
Technology and Innovation: The tube mill industry is continuously evolving, with new technologies enhancing production efficiency and product quality. Partnering with a supplier that invests in innovation can give your business a competitive edge.
Cost-Effectiveness: While quality is paramount, it’s also essential to consider the cost-effectiveness of the tube mill. Evaluate the total cost of ownership, including maintenance and operational costs, when making your decision.
Customer Reviews and Testimonials: Research customer reviews and testimonials to gauge the reputation and reliability of potential suppliers. This can provide valuable insights into their performance and customer satisfaction.
Conclusion
Understanding the tube mill process and the steps involved in manufacturing steel pipes is crucial for anyone in the industry. By selecting the right tube mill supplier, you can ensure the success of your production line and maintain a competitive edge in the market. With the right equipment, expertise, and support, you can produce high-quality steel pipes that meet the demands of various industries.
Products
- 457mm FFX ERW Tube Mill
- 34mm*6.5mm Pipe Mill
- Roller Quick Change System Tube Mill
- Large Diameter Direct Forming Square Tube Mill
- TD 38 Tube Mill(12-38mm)
- TD 50 Tube Mill(25-63mm)
- TD 76 Tube Mill(32-89mm)
- TD 114 Tube Mill(42-119mm)
- TD 127 Tube Mill(42-127mm)
- TD 219 Tube MIll(89-219mm)
- TD 273 Tube MIll(114-273mm)
- TD 325 Tube MIll(127-325mm)
- Slitting Line
- Cut to Length Line
- Cold Roll Forming Machine
Related Products
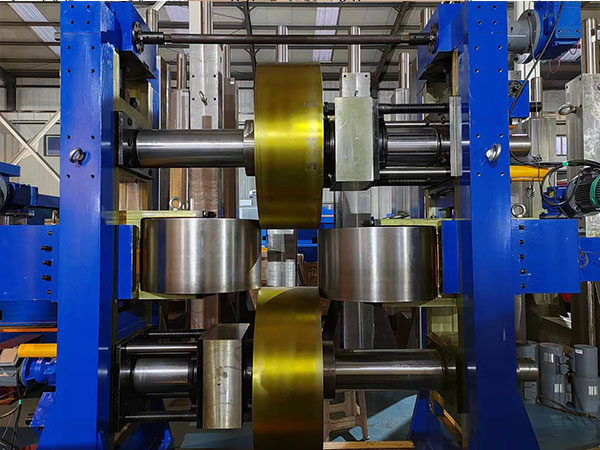