DFT Square Tube Mill Technology
1. Overview of DFT Pipe Mill Technology
1.1 What is DFT Pipe Mill?
DFT (Direct Forming Technology) is an advanced technology used in pipe mill manufacturing. In contrast to traditional methods, which typically involve more complex processes and higher material costs, DFT offers a streamlined solution that not only reduces material consumption but also lowers production costs. This article will explore the concept of DFT, compare it with the traditional round-to-square forming method, and analyze how it contributes to material and roller savings. Using the example of a 30×30×2mm square tube, it was demonstrated that DFT can save up to 6 mm of material compared to the traditional round-to-square forming method.
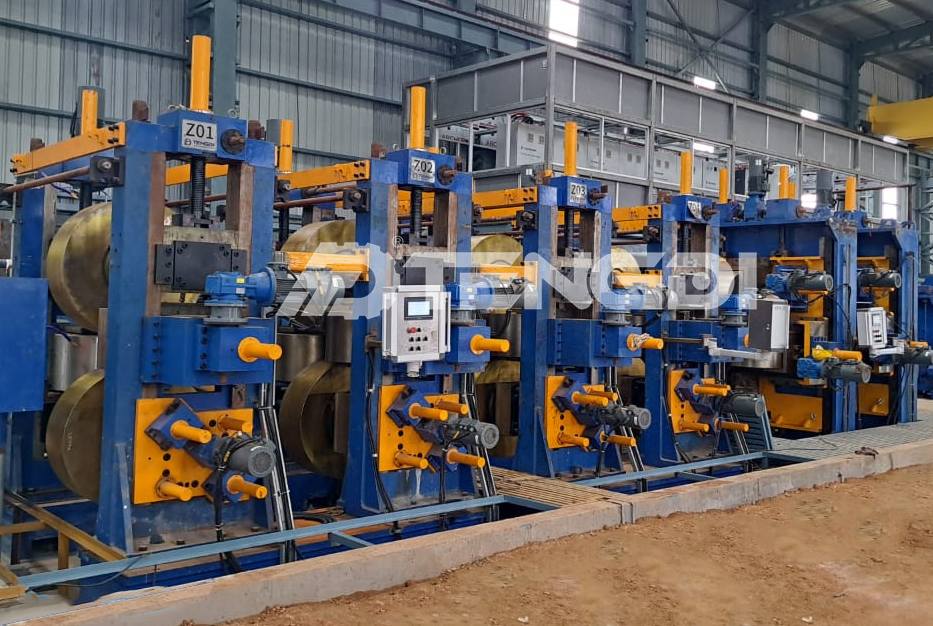
2. DFT in Steel Structure
2.1 DFT Structural Steel Tube
In structural steel applications, DFT allows for the efficient production of steel tubes that are used in construction projects. These tubes are typically used in the framing of buildings, bridges, and other infrastructure. DFT’s direct-forming capabilities enable the production of steel tubes that are not only cost-effective but also meet high strength and durability standards required for structural applications.
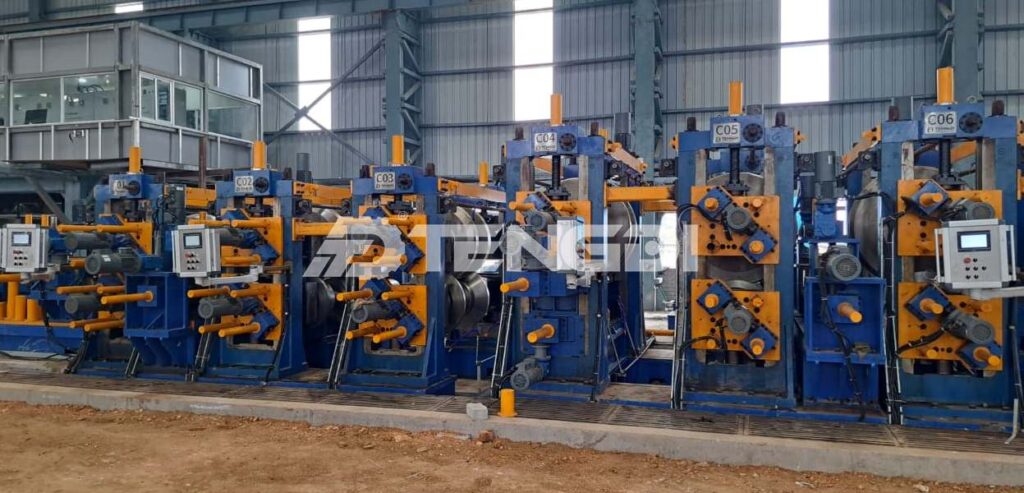
3. Comparison of Round-to-Square Forming vs. DFT Direct Forming
3.1 Round-to-Square Forming Process
The traditional round-to-square forming method involves taking a round pipe and transforming it into a square tube. Each specification requires a separate set of molds, leading to higher operational costs.
Product Range:
Round-to-Square: Suitable for pipes with a normal diameter and wall thickness, typically with a thickness-to-diameter ratio between 2% and 7%. It works for low-carbon steels and low-alloy steels (material not exceeding Q345). Round-to-square units can produce both round and square pipes.
Direct Forming: Typically used for pipes with a minimum diameter of 50mm and a minimum wall thickness of 3mm. The largest direct-forming units in China can produce pipes with diameters up to 500mm and wall thicknesses up to 20mm. Direct-forming units are specialized machines that produce only square and rectangular tubes, and they can also produce open-profile steel.
Performance Characteristics:
Round-to-Square: The corners of the square pipe are thickened, giving it higher mechanical strength.
Direct Forming: The corners of the square pipe are thinner, which may lead to weaker strength at the corners. However, direct forming provides better material efficiency.
3.2 DFT Direct Forming Technology
The key advantage of DFT is its ability to use combination molds that cover multiple sizes. This not only reduces material waste but also leads to cost savings in terms of mold and die requirements. Since DFT eliminates the need for multiple molding stages, the process becomes more efficient and environmentally friendly.
Material Savings:Direct forming can save up to 4% of the strip material compared to round-to-square methods.
Energy Consumption:DFT consumes less energy than round-to-square forming because it involves less deformation. The direct forming process only requires minimal contact between the steel strip and the forming tool, which results in a lower deformation force and reduced power consumption.
Pipe Profile:
Round-to-Square: The adjustment of the pipe profile is relatively easy, and the angles of the square tube are even.
Direct Forming: The profile adjustment requires higher expertise, and achieving uniformity in the four corners can be more challenging.
Equipment Investment:
Direct Forming: The equipment investment for direct forming is generally higher, ranging from 30% to 40% more than round-to-square forming due to the specialized machinery and molds required.
Mold Investment:
Round-to-Square: A separate mold is required for each specification of the tube.
Direct Forming: DFT uses combination molds that can cover a wider range of specifications, reducing the need for multiple sets of molds.
3.3 Roller Savings
Another significant benefit of DFT is its ability to reduce tube mill roller costs:
Round-to-Square Forming: In the traditional method, each size requires a separate mold and roller set, which increases the capital investment and maintenance costs.
DFT Direct Forming: DFT uses combination molds that cover a wide range of sizes, reducing the need for multiple sets of rollers and molds. This not only saves money but also improves the flexibility of the production process.
5. Actual case of our company DFT Square tube mill Technology
Our equipment has a diameter range from 180*180mm to 350*350mm, and a thickness range from 5.0mm to 14.0mm, which fully meets the requirements of customers. It has been running smoothly in India.
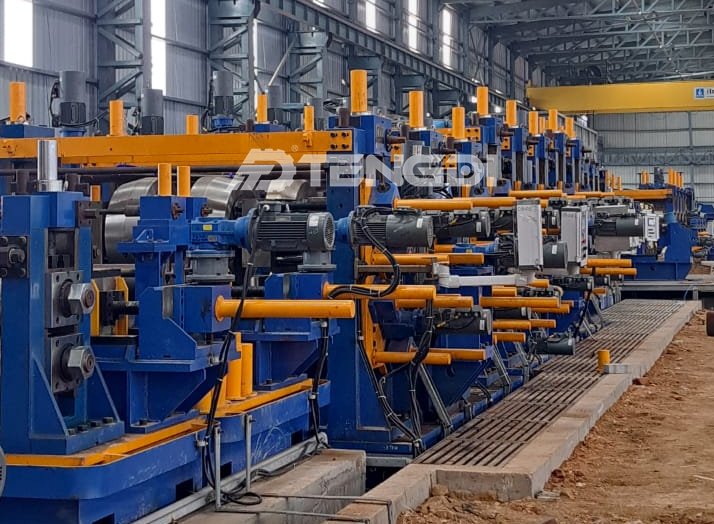
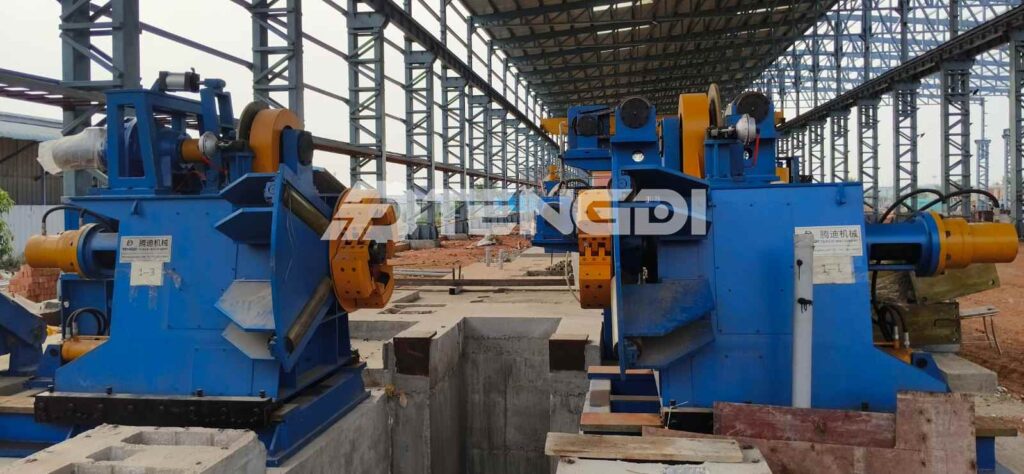
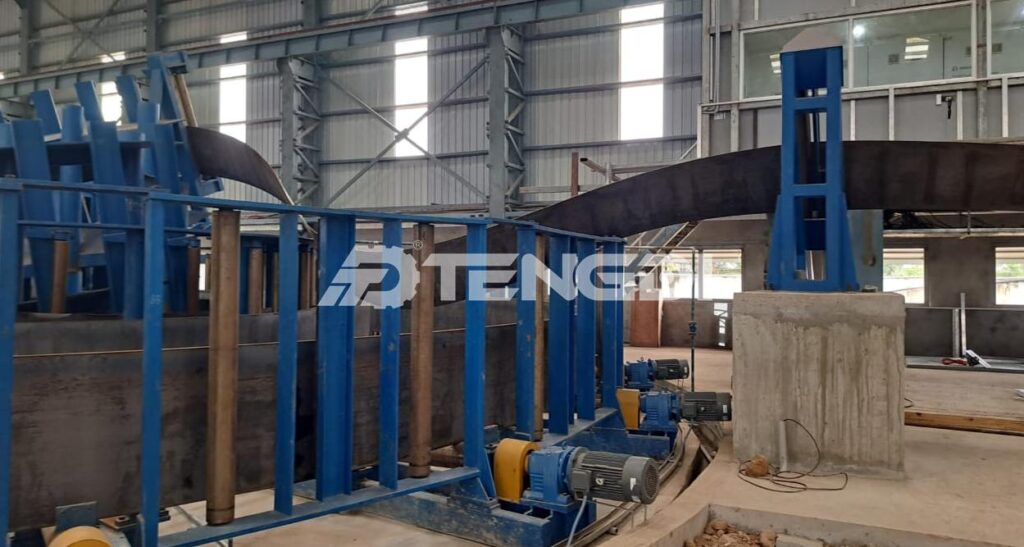