Continuous Galvanizing Line: Manufacturing Hot-Dip Galvanized Steel Pipes
You are here: Home>Industry Information> Continuous Galvanizing Line: Manufacturing Hot-Dip Galvanized Steel Pipes
Introduction
In today’s industrial landscape, the demand for durable, corrosion-resistant steel pipes continues to grow. One of the most effective ways to protect steel from rust and corrosion is through galvanization, specifically using a continuous galvanizing line. This advanced manufacturing process ensures that steel pipes are coated with a protective layer of zinc, making them ideal for a wide range of applications. In this article, we will explore the continuous galvanizing line, the manufacturing process of hot-dip galvanized steel pipes, and why our solutions stand out in the market.
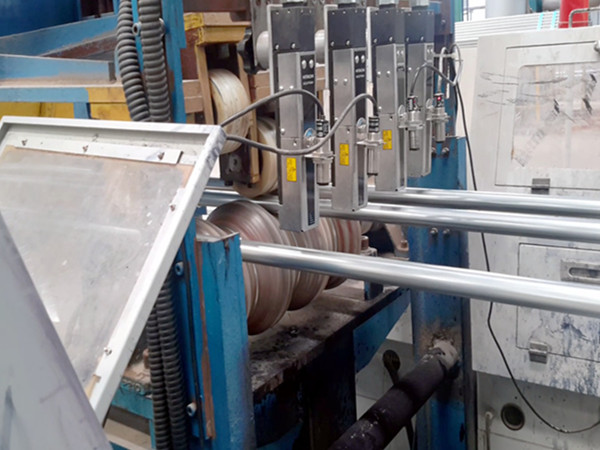
What is a Continuous Galvanizing Line?
A continuous galvanizing line is a state-of-the-art production system designed to coat steel pipes with zinc in a continuous process. Unlike batch galvanizing, where individual pieces are dipped into molten zinc, the continuous method allows for uninterrupted production, enhancing both efficiency and consistency.
Key components of a continuous galvanizing line include:
- Pre-treatment and cleaning units: Ensure that the steel surface is free from impurities.
- Zinc pot and coating section: Where steel pipes are immersed in molten zinc for coating.
- Cooling and post-treatment units: Stabilize the zinc layer and ensure quality.
The continuous process minimizes downtime and increases production speed, making it ideal for large-scale manufacturing of galvanized steel pipes.
Manufacturing Process of Hot-Dip Galvanized Steel Pipes
The hot-dip galvanizing process involves several critical steps:
Pre-treatment and Cleaning: The steel pipes undergo a thorough cleaning process to remove any dirt, grease, or oxidation. This ensures that the zinc adheres properly to the steel surface.
Fluxing: After cleaning, the pipes are treated with a flux solution that prevents oxidation before they are immersed in the zinc bath.
Zinc Bath Immersion: The cleaned and fluxed pipes are then submerged in a molten zinc bath at temperatures of around 450°C (842°F). This hot-dip process forms a robust, corrosion-resistant layer on the surface of the steel.
Cooling and Inspection: After coating, the pipes are cooled in a controlled manner to solidify the zinc layer. Each pipe undergoes a rigorous inspection to ensure that the coating is uniform and meets quality standards.
Post-Galvanizing Treatment: This may include additional processes such as passivation or oiling to enhance the durability of the coating.
By following these steps, the steel pipes produced are highly resistant to corrosion and have a long service life, even in harsh environments.
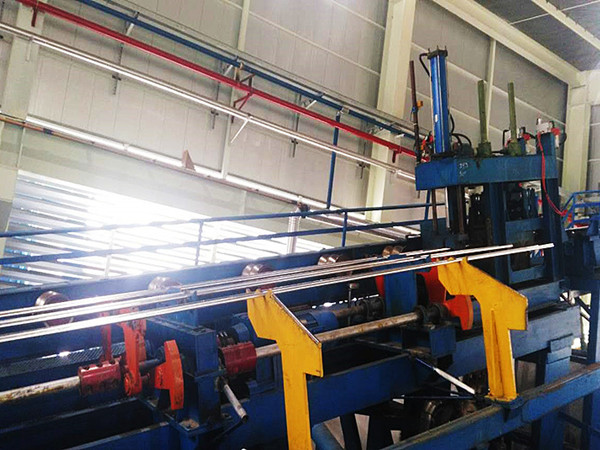
Advantages of Using a Continuous Galvanizing Line
Opting for a continuous galvanizing line offers several advantages:
- High Efficiency: Continuous production eliminates delays and reduces operational costs, making it a cost-effective solution for large-scale manufacturing.
- Consistent Quality: Automated control systems ensure uniform coating thickness and quality across all pipes.
- Environmental Benefits: Modern galvanizing lines are designed with energy-efficient technologies that reduce waste and lower energy consumption.
These benefits make continuous galvanizing lines a preferred choice for industries that require high-quality galvanized steel pipes on a large scale.
Applications of Hot-Dip Galvanized Steel Pipes
Hot-dip galvanized steel pipes are widely used in various industries due to their durability and corrosion resistance. Common applications include:
- Construction: Galvanized pipes are essential in structural applications such as scaffolding, fencing, and building frameworks.
- Automotive: The automotive industry relies on galvanized steel for exhaust systems, chassis components, and other parts exposed to harsh conditions.
- Agriculture: Galvanized steel pipes are used in irrigation systems, livestock enclosures, and other agricultural infrastructure.
- Utilities: Water and gas distribution systems benefit from the long-lasting nature of galvanized pipes.
The versatility of hot-dip galvanized steel pipes makes them a go-to choice for multiple sectors, ensuring longevity and reliability.
Why Choose Our Continuous Galvanizing Line?
At TENGDI Machinery, we pride ourselves on providing cutting-edge continuous galvanizing lines that meet the highest industry standards. Here’s why our solution stands out:
- Advanced Technology: Our continuous galvanizing lines incorporate the latest innovations, ensuring precise control over the galvanizing process and delivering consistent results.
- Customization Options: We understand that every client has unique needs. Our lines can be tailored to meet specific production requirements, from line speed to coating thickness.
- Proven Track Record: With years of experience in the industry, we have successfully implemented continuous galvanizing lines for clients worldwide. Our satisfied customers testify to the quality and reliability of our equipment.
Technical Specifications and Customization Options
Our continuous galvanizing lines offer a range of technical specifications to suit different production needs, including:
- Production Capacity: Up to 600,000 tons per year.
- Line Speed: Adjustable speeds from 30 to 120 meters per minute.
- Zinc Coating Thickness: Options ranging from 40 to 275 grams per square meter.
In addition to standard models, we provide customization options, allowing you to adapt the line to your specific requirements.
Conclusion
In conclusion, a continuous galvanizing line is a highly efficient and reliable method for manufacturing hot-dip galvanized steel pipes. At TENGDI Machinery, we offer state-of-the-art solutions that deliver consistent quality and long-lasting performance. If you are looking to enhance your production capabilities with a continuous galvanizing line, contact us today to learn more about how we can meet your needs.
Products
- 457mm FFX ERW Tube Mill
- 34mm*6.5mm Pipe Mill
- Roller Quick Change System Tube Mill
- Large Diameter Direct Forming Square Tube Mill
- TD 38 Tube Mill(12-38mm)
- TD 50 Tube Mill(25-63mm)
- TD 76 Tube Mill(32-89mm)
- TD 114 Tube Mill(42-119mm)
- TD 127 Tube Mill(42-127mm)
- TD 219 Tube MIll(89-219mm)
- TD 273 Tube MIll(114-273mm)
- TD 325 Tube MIll(127-325mm)
- Slitting Line
- Cut to Length Line
- Cold Roll Forming Machine
Related Products
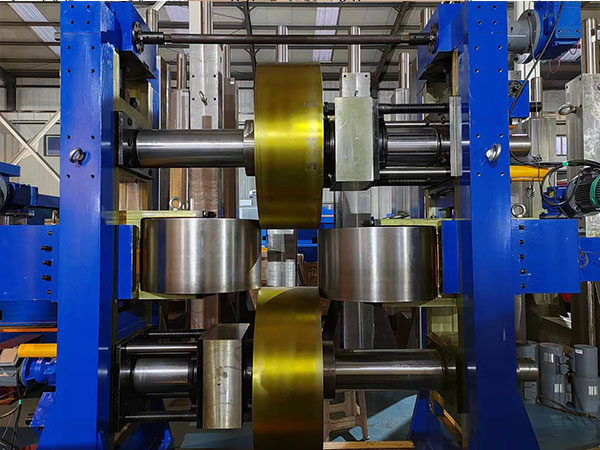