Understanding Hot Dip Galvanizing: Meaning and Production Line
You are here: Home>Industry Information> Understanding Hot Dip Galvanizing: Meaning and Production Line
What is Hot Dip Galvanizing?
Hot dip galvanizing involves immersing steel or iron in molten zinc to create a durable and protective coating. This process is highly effective in preventing corrosion and extending the lifespan of metal products. The term “hot dip galvanized” refers not only to the process but also to the protective qualities the coating provides. Hot dip galvanized pipes are widely used in industries like construction, automotive, and infrastructure due to their durability and long-term performance.
Compared to other methods such as electro galvanizing and chemical dip, hot dip galvanizing offers a thicker and more uniform zinc coating. While electro galvanizing applies zinc through an electric current, it typically results in a thinner layer, making it less durable in harsh environments.
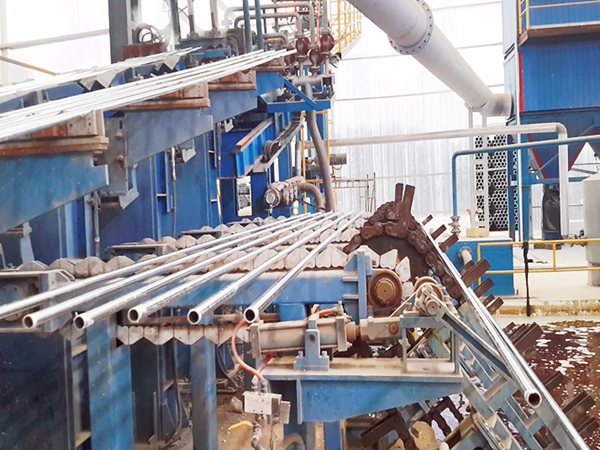
Hot Dip Galvanizing vs. Electro Galvanizing
Understanding the differences between hot dip galvanizing and electro galvanizing is essential for selecting the right method for specific applications. Below is a table that highlights the key differences between these two methods:
Feature | Hot Dip Galvanizing | Electro Galvanizing |
---|---|---|
Coating Process | Dipping metal into molten zinc | Applying zinc through an electric current |
Coating Thickness | Thicker and more rugged coating | Thinner, more uniform coating |
Durability | Highly durable, suitable for outdoor and heavy-duty applications | Less durable, best for indoor or less demanding environments |
Corrosion Resistance | Superior corrosion protection | Moderate corrosion protection |
Surface Finish | Rougher finish, with visible zinc spangles | Smoother, shinier finish |
Cost | Generally higher due to thicker coating and material use | Lower cost, but may require more frequent maintenance |
Applications | Ideal for construction, infrastructure, and automotive sectors | Suitable for indoor furniture, appliances, and light-duty uses |
This table provides a clear comparison of hot dip galvanizing and electro galvanizing, helping you choose the right method based on your specific needs.
The Role of Auto Dipping in Hot Dip Galvanizing
Auto dipping is an advanced technique used in hot dip galvanizing to automate the immersion process. This method ensures that the metal is coated uniformly and consistently, minimizing human error and improving efficiency. Auto dipping is particularly advantageous in large-scale production, where speed and precision are critical.
By incorporating auto dipping into the galvanizing process, manufacturers can achieve higher throughput while maintaining the quality of the coating. This method is especially beneficial for industries requiring mass production of galvanized pipes, as it reduces production time and costs.
Hot Dip Galvanizing Pipe Production Line
Hot dip galvanized pipes are utilized across various industries due to their corrosion resistance and durability. Some common applications include:
- Construction: Structural components, scaffolding, and pipelines.
- Automotive: Exhaust systems, chassis components, and frames.
- Infrastructure: Water supply systems, bridges, and guardrails.
The versatility of hot dip galvanized pipes makes them a preferred choice in many sectors, where long-term performance and cost-effectiveness are essential.
Applications of Hot Dip Galvanized Pipes
When investing in a slitting line, it’s essential to consider several key features that determine the quality and performance of the equipment:
- Durability and Longevity: High-quality slitting lines are built to last, with robust components that withstand the rigors of daily operation.
- Precision Cutting: The ability to cut metal sheets with high accuracy ensures that the final product meets exact specifications.
- Customization: Slitting lines should be adaptable to different materials and widths, offering flexibility to meet various production needs.
- Efficiency: Efficient slitting lines minimize downtime and maximize output, contributing to overall productivity.
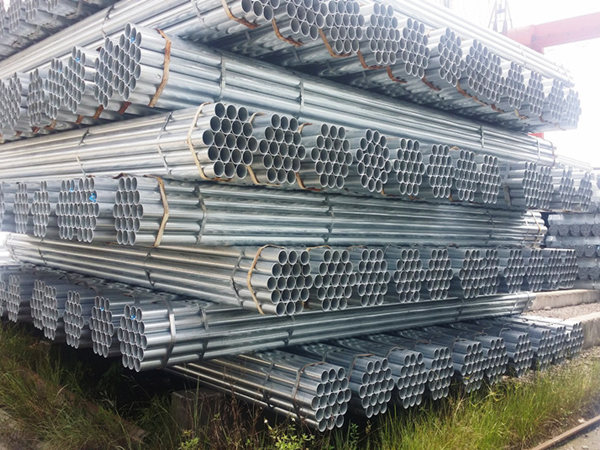
Conclusion
Hot dip galvanizing is a vital process for protecting metal products from corrosion, with hot dip galvanized pipes playing a critical role in many industries. By choosing a high-quality production line from a trusted manufacturer like us, you can ensure that your products meet the highest standards of durability and performance.
If you’re looking to invest in a hot dip galvanizing pipe production line, don’t hesitate to contact us for more information or to discuss your specific needs. We’re here to provide the best solutions for your business.
Products
- 457mm FFX ERW Tube Mill
- 34mm*6.5mm Pipe Mill
- Roller Quick Change System Tube Mill
- Large Diameter Direct Forming Square Tube Mill
- TD 38 Tube Mill(12-38mm)
- TD 50 Tube Mill(25-63mm)
- TD 76 Tube Mill(32-89mm)
- TD 114 Tube Mill(42-119mm)
- TD 127 Tube Mill(42-127mm)
- TD 219 Tube MIll(89-219mm)
- TD 273 Tube MIll(114-273mm)
- TD 325 Tube MIll(127-325mm)
- Slitting Line
- Cut to Length Line
- Cold Roll Forming Machine
Related Products
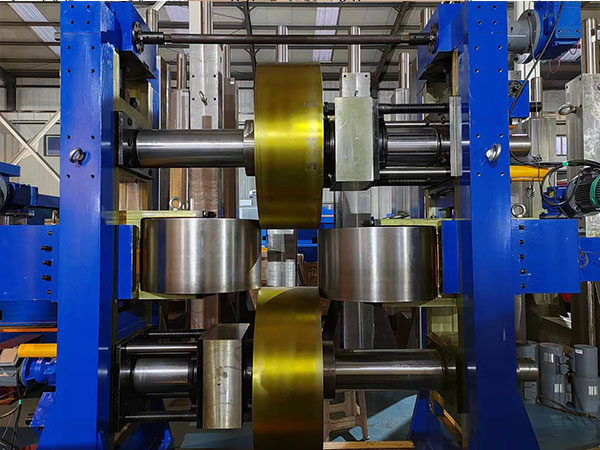